Карбід титану — Вікіпедія
Карбід титану | |
---|---|
![]() | |
Назва за IUPAC | Титан карбід |
Ідентифікатори | |
Номер CAS | 12070-08-5 |
Номер EINECS | 235-120-4 |
SMILES | [CH3-].[Ti][1] |
InChI | InChI=1S/CH3.Ti/h1H3;/q-1; |
Властивості | |
Молекулярна формула | TiC |
Молярна маса | 59,89 г/моль |
Молекулярна маса | 60 а. о. м. |
Зовнішній вигляд | сіро-чорний порошок |
Густина | 4,92 г/см³ |
Тпл | 3257 °C |
Ткип | 4820 °C |
Розчинність (вода) | 10 мг/л |
Структура | |
Кристалічна структура | кубічна решітка типу NaCl |
Координаційна геометрія | восьмигранна |
Геометрія | α=0,430-0,433 нм |
Термохімія | |
Ст. ентальпія утворення ΔfH 298 | -209 кДж/моль |
Ст. ентропія S 298 | 24,7 Дж/(моль • К) |
Теплоємність, c p | 34,23 Дж/(моль • К) |
Небезпеки | |
ГДК (Україна) | 10 мг/м3 |
Якщо не зазначено інше, дані наведено для речовин у стандартному стані (за 25 °C, 100 кПа) | |
Інструкція з використання шаблону | |
Примітки картки |
Карбі́д тита́ну — хімічна сполука елементів титан і карбон із формулою TiC. Це поширений матеріал з високою температурою плавлення, високою твердістю (9—9,5 за шкалою Мооса), низьким електроопором, високою теплопровідністю, стійкістю до агресивних середовищ і до абразивного зношування.
Застосовується переважно в твердих сплавах, виробництві високоякісних інструментів, як покриття для поліпшення властивостей матеріалів тощо.

Як сполука карбід титану відомий близько ста років. За цей час докладно вивчено традиційні способи його отримання, фізичні, механічні та хімічні властивості матеріалу. В історії карбіду титану сталися три знаменні події, що призвели до збільшення в сотні разів його використання в техніці матеріалів.
Це, по-перше, розробка і швидкий розвиток промислового випуску безвольфрамових твердих сплавів на основі карбіду титану. Зараз останні ще поступаються за деякими показниками вольфрамовмісним твердим сплавам і не в усіх випадках можуть їх замінити. Однак безперервне вдосконалення твердих сплавів на основі карбіду титану й постійно зростаюча дефіцитність вольфраму роблять цей напрямок у застосуванні карбіду титану вельми перспективним.
По-друге, в окремий технічний напрямок виділилося нанесення на інструментальні, конструкційні та інші вироби покриття з карбіду титану. Розроблено приблизно десяток різних промислових методів нанесення покриттів із карбіду титану.
По-третє, карбід титану все ширше застосовується в абразивних матеріалах.
Понад 80% карбіду титану у виробничих умовах отримують із діоксиду титану (в основному через порівняно низьку вартість і доступність TiO2).
Протягом останніх років вуглетермічний метод утримує панівне становище у виробництві карбіду титану. Головні причини — відпрацьована технологія, стандартне й недороге обладнання, порівняно дешева сировина.

У цьому процесі суміш, що складається з 68,5% TiO2 і 31,5% сажі, піддається тривалому й ретельному перемішуванню в рідкому середовищі. Для зменшення часу приготування суміші в чотири рази рекомендується проводити процес у вакуумі[2]. Суміш TiO2 із сажею набивається в графітовий патрон або пресується під тиском 1,5 • 107 Па у брикети, які завантажуються в графітові човники або тиглі. Карбідизація суміші здійснюється в атмосфері водню у вугільно-трубчастих печах опору, у власній захисній атмосфері у вертикальних або вакуумних печах. У вугільно-трубчастих печах графітові човники безперервно просуваються в печі, температура якої 2000 °С. Подрібнений і просіяний карбід титану містить загалом від 20 до 20,5% вуглецю, з яких 1,0-2,0% перебуває у вільному (хімічно несполученому) стані.
При вакуумній карбідизації реакція утворення TiC починається вже при 800 °С і швидко відбувається при 1200–1400 °С. Остаточна витримка тривалістю 0,5 год здійснюється при 1900–1950 °С. Карбід титану після подрібнення й просіювання містить від 19,5 до 20,3% вуглецю, 0,1-0,8% від загальної кількості перебуває у вільному стані.
Отримати карбід титану зі ступенем перетворення, близьким до одиниці, можна вже при 1900 °С, а при температурі вище 3070 °С, тобто вище температури плавлення TiC, спостерігається помітний тиск парів титану. Енерговитрати на утворення карбіду титану при 1200-3070 °С зростають лінійно.
Отримання карбіду титану з діоксиду титану відбувається в декілька стадій відповідно до існування ряду оксидів титану: TiO2 → Ti2O3 → TiO → TiC. Остання стадія процесу ускладнюється утворенням безперервного ряду твердих розчинів TiO-TiC.
Були спроби отримати порошок карбіду титану з діоксиду за допомогою плазмохімічного синтезу в дуговій плазмі в середовищі аргону й водню[3]. Змінюючи умови синтезу, можна отримати карбід титану з вмістом зв'язаного вуглецю 10-20%.
Вуглетермічним методом виробляється більша частина загального випуску карбіду титану, але розроблено кілька методів, здатних конкурувати з цим способом як за економічними, так і за якісними показниками.

Виробництво карбіду титану з суміші порошку титану з сажею залежно від технологічних умов може здійснюватися кількома способами:
- прямим синтезом без плавлення титану,
- псевдоплавленням;
- методом високотемпературного синтезу.
Прямий синтез зазвичай здійснюється в лабораторних умовах із метою отримання карбіду титану з заданим вмістом зв'язаного вуглецю при мінімальному вмісті вільного вуглецю і кисню. Карбідизація здійснюється при залишковому тиску 10−2−10−3 Па й для отримання стехіометричного карбіду титану потрібне додавання в шихту додаткової кількості титану (понад стехіометричне співвідношення Ti і С) для компенсації його втрат внаслідок випаровування. Високоякісний карбід титану можна отримати вже при 1600 °С. Спроби отримати якісний карбід титану із суміші титану з вуглецем при високих тисках (1-7) • 109 Па дали негативний результат. Встановлено, що вміст вільного вуглецю збільшується зі збільшенням тиску[4][5].
Псевдоплавлений карбід титану одержують взаємодією розплавлених частинок титану з сажею. Нагрівання суміші порошку титану з сажею, спресованою під тиском (1,5-1,6) • 107 Па у брикети діаметром і висотою 30-50 мм здійснюється за двоступінчастим режимом: поступовий підйом до температури 900 °С зі швидкістю 35-40 °С/хв, з подальшим пересуванням зразків у зону з температурою 2050 °С, яку вони долають за 25 хвилин. Хімічний склад отриманого TiC: вміст зв'язаного вуглецю 18,5-19,9%; вільного 0,1-0,4%; кисню 0,1-0,3%[6].
Розроблено велику кількість модифікацій цього методу одержання карбіду титану, що відрізняються між собою як за використанням початкових реагентів, так і за технологічними умовами процесу[7]. Цим методом можна отримувати покриття, монокристали й волокна з карбіду титану.
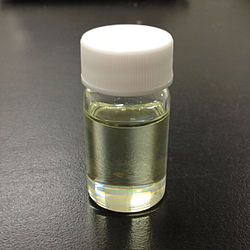
Як галогеніди використовують TiCl4 або TiI4, а вуглецьвмісні компоненти можуть бути різними: вуглеводні, феноли і т. д. Найчастіше використовуються метан CH4, етен C2H4, CCl4 і бензол C6H6.
Найчастіше використовується суміш TiCl4 + CH4 + H2. Попри те, що вихід порошку TiC значно зростає (з 5 до 15%) при заміні тетрахлориду титану[ru] тетрайодидом титану[en], у виробничих умовах останній майже не використовується через його велику вартість[8].
Для утворення карбіду титану необхідно вести процес на ділянці температур 1200–1500 °С.
Вихід продукту збільшується зі зростанням концентрації метану, але водночас підвищується вміст вільного вуглецю. Для збільшення виходу карбіду титану рекомендується вводити в реакційну суміш невеликі кількості WCl6 або MoCl5, які стимулюють процес гомогенного зародження частинок, і пропускати вздовж реакційних трубок інертний газ щоб запобігти утворенню відкладень. Однак кардинальним вирішенням проблеми є здійснення процесу при вищих температурах, наприклад з використанням плазми.
Плазмохімічним методом отримують ультрадисперсні порошки карбіду титану з унікальними властивостями. Плазмохімічний синтез забезпечує високу продуктивність процесу, оскільки в умовах низькотемпературної плазми реакція утворення карбіду титану відбувається практично миттєво (10−2−10−6 с). До переваг цього методу належить простота технологічних схем і можливість створення замкнутих циклів[9].
Як вуглецьвмісні компоненти можуть використовуватися метан, етан, бензен, бензин, толуен, чотирихлористий вуглець, галогензаміщені алкани й алкени, ароматичні вуглеводні[10], але найчастіше використовують бензол і чотирихлористий вуглець. У цьому випадку спостерігається велика однотипність процесів синтезу TiC[11].
Плазмохімічні порошки карбіду титану (розмір часток 0,02-0,35 мкм) зазвичай мають склад, %: зв'язаний вуглець 18; вільний вуглець 1,5; кисень 1,4.
Плазмохімічний синтез технологічно складний (дуже високі температури синтезу, значна реакційна здатність і токсичність галогенідів титану), тому його використання при синтезі карбіду титану не завжди виправдане.
Використання відходів металообробного виробництва як вихідної сировини дозволяє значно знизити вартість карбіду титану. Крім того, промислове освоєння переробки відходів титану в карбід дозволить частково вирішити актуальну задачу, пов'язану з утилізацією некондиційних відходів титану та його сплавів.
Основну частину некондиційних відходів становить сильноокиснена, забруднена рештками мастила й осколками твердосплавного інструменту стружка титану та його сплавів. Ефективної технології переробки таких відходів досі немає[12].
Технологія утилізації некондиційних відходів титану та його сплавів шляхом виробництва з них порошку карбіду титану, крім усього іншого, має наступну перевагу: значно спрощується технологічна схема підготовки відходів до переробки, оскільки непотрібне попереднє відновлення окисненої стружки і відділення від неї осколків твердосплавного інструменту.
Карбід титану отримують зі стружки титанових сплавів двома методами: 1) гідрогенізацією стружки, її подрібненням, дегідрогенізацією і карбідизацією, 2) карбідизацією суміші титанової стружки із сажею.

Вміст зв'язаного вуглецю в карбіді титану, отриманому зі стружки за схемою гідрогенізація → розмел → змішування з сажею → карбідизація, зазвичай не перевищує 17,6%, а вміст вільного вуглецю становить 1,4-2,3%. Іншими недоліками цього методу є значна тривалість процесу та використання вибухонебезпечних речовин.
Як вихідний компонент для виробництва карбіду титану можна використовувати стружку не тільки технічно чистого титану (сплав BTI-O), а й легованих Al, V, Cr, Mo, Zr та іншими елементами титанових сплавів. При цьому режими карбідизації в основному не змінюються[13]. Вміст легуючих елементів в отриманому карбіді титану практично не змінюється в порівнянні з їх вмістом у початковій стружці.
Карбід титану невисокої вартості можна отримувати і з бідних титанових руд, наприклад ільменіту або перовськіту (CaTiO3). Розроблений у США процес виробництва карбіду титану з титановмісної сировини зі значною кількістю СаО включає такі операції:
- Вибіркове відновлення оксидів заліза з ільменіту з подальшим виділенням заліза і отримання таким чином CaTiO3-шлаку з низьким вмістом Fe.
- Перетворення або титанового шлаку, або концентрату перовскіту на суміш карбідів титану і кальцію з подальшою екстракцією карбіду титану шляхом вимивання CaC2 водою з утворенням ацетилену та вапна (Са(ОН)2), яке легко відділяється.
Отриманий карбід титану містить значну кількість СаО, Fe, SiO2, Al2O3, тому він використовується тільки як сировина для виробництва тетрахлориду титану[14].
Карбід титану утворюється й при електроерозійній обробці титану в діелектричній рідині (наприклад, у трансформаторному мастилі)[15].
Монокристали TiC виготовляють декількома методами: рідкофазним, шляхом розчинення й плазмохімічним синтезом.
Рідкофазним методом отримують найчистіші та найбільші монокристали карбіду титану[16].
Метод отримання монокристалів карбіду титану плавленням не здобув широкого застосування через високі енергетичні витрати й складність апаратури.
Одним із енергоекономічних методів отримання монокристалів TiC є метод розчинення, який полягає у взаємодії розчинених у металевих або сольових розплавах атомів різних сполук титану й вуглецю з утворенням карбіду титану. Як розчинник застосовують залізо, кобальт, нікель, алюміній і магній[17].
Волокна з карбіду титану отримують осадженням із газової фази, яка складається із TiCl4 + СхНу (пропан) + Н2; TiCl4 + CCl4 + Н2 або TiCl4 + nC3Н8(С6Н6) + Н2[18][19][20]. Карбід титану може осаджуватись на графіті, молібдені, вольфрамі, кераміці при температурах 800–1600 °С, що визначаються складом газової суміші та матеріалом основи.
Тривалість одного циклу становить 0,5-4 год, а тиск у камері 105 Па.
Волокна карбіду титану з мінімальною кількістю дефектів отримують із найменш перенасичених середовищ, але в цьому випадку швидкість росту волокон сповільнюється.
Ниткоподібні кристали карбіду титану отримують шляхом протягування дроту через реактор, а також із суміші TiCl4 + CCl4 + Н2 при температурах 1250–1350 °С. У другому випадку довжина кристалів досягає 3 мм, а діаметр — 20 мкм.
Карбід титану є досить стабільною сполукою, свідченням чого служать високі температура плавлення і теплота утворення.
Теплопровідність карбіду титану при температурі нижче −173 °С збільшується із зростанням його дефектності за вуглецем[21], а при вищих температурах відмінність у теплопровідності карбіду титану в області гомогенності нівелюється.
Коефіцієнт теплового розширення й питомий опір карбіду титану зростають зі збільшенням його дефектності за вуглецем, у той час як для абсолютного значення коефіцієнта Холла, коефіцієнта термо-е.р.с. і термічного коефіцієнта електроопору спостерігається протилежна картина. Таке зростання електроопору і коефіцієнта Холла зі збільшенням температури свідчить про металічний характер провідності карбіду титану.
Карбід титану має порівняно низьку роботу виходу електрона, яка різко зменшується зі зменшенням вмісту зв'язаного вуглецю[22].
Молярна магнітна сприйнятливість карбіду титану при 20 °С змінюється залежно від його дефектності за вуглецем у десятки разів (наприклад, до 10б для TiC0,95 становить ~ 5, а для TiC0,70 ~ 100).
Коефіцієнт випромінювання карбіду титану в температурному інтервалі 1500–2400 °С становить ~ 0,7 Вт/(м2·К4)[22]. Для порівняння коефіцієнт випромінювання "сірого тіла" знаходиться в межах 0 < C < 5,7, а коефіцієнт випромінювання абсолютно чорного тіла становить 5,7 Вт/(м2·К4).
Після обробки карбіду титану цезієвою плазмою робота виходу електрона не змінюється, що свідчить про відсутність взаємодії TiC із плазмою[23]. З іншого боку, під дією нейтронного опромінення в зразках з карбіду титану TiC0,94 відзначено значне збільшення електричного опору й параметра решітки (сторона куба), збільшення об'єму на 0,3-0,5%[24].
Міцність карбіду титану залежить головним чином від пористості досліджуваних зразків і значно менше позначаються: дефектність TiC за вуглецем, спосіб виготовлення і розмір зерен зразків. Наприклад, зі збільшенням пористості зразків карбіду титану на 5% їх міцність зменшується вдвічі[22].
Деталі з карбіду титану погано зварюються. Найкращі результати отримано при дифузійному зварюванні зразків з карбіду титану в режимі: температура 1800 °С, тривалість 10 хвилин, залишковий тиск не більше 10 Па при питомому тиску 10 кПа[25].
Карбід титану стійкий до дії соляної, сірчаної та фосфорної кислот і лугів, але розчиняється в царській воді й суміші азотної і плавикової кислот. Зі збільшенням дефектності за вуглецем карбід титану стає менш стійким у розчинах фосфорної і соляних кислот, що містять перекис водню.
Карбід титану має високу корозійну стійкість на ділянці потенціалів негативніше 0,05 у лужних і 0,7 — у кислих розчинах.

Взаємодія карбіду титану з іонами водню, що розряджаються на його поверхні, полегшується при збільшенні дефіциту вуглецю в TiC. Зі зміною вмісту зв'язаного вуглецю в карбіді титану при рівних умовах катодної поляризації утворюються різні сполуки карбіду титану з воднем: або тверді розчини водню в карбіді титану (карбогідриди змінного складу за воднем) або гідриди TiH2 і TiH. У перших двох випадках надалі водень може бути легко виведений з карбіду титану без руйнування його кристалічної решітки[26].
Для виробництва спечених виробів на основі карбіду титану безсумнівний інтерес представляють дані про змочуваність карбіду титану різними металами. Найбільш повної змочуваності можна досягти при використанні нікелю в аргоні і кобальту у вакуумі. Ці метали і найчастіше використовуються в твердих сплавах на основі TiC як зв'язка.
Карбід титану має досить високу стійкість проти окиснення. Інтенсивне окиснення TiC починається при температурах вище 1100 °С[27]. При окисненні карбіду титану на початковій стадії утворюється твердий розчин TiC-TiO, який перешкоджає подальшому окисненню. При температурах понад 1100 °С кисень дифундує через шар твердого розчину, утворюючи TiO[28].
При температурах вище 40 °С в середовищі хлору з карбіду титану утворюється хлорид титану, а в середовищі фтору — фторвуглецеві сполуки.
При високих температурах водяна пара окиснює карбід титану в атмосфері CO2 або N2O. TiC розпадається, утворюючи діоксид титану[28].
Понад 95% усього карбіду титану, що виготовляється у світі, іде на виробництво твердих сплавів[29].
Починаючи з 30-х років карбід титану почали вводити в тверді сплави системи WC-Со для підвищення твердості й зниження ямкового зношення. Фірма Firth Sterling Steel Corp. (США) випустила на світовий ринок сплави на основі системи WC-TaC-TiC-Со. Оскільки запаси танталу в Європі незначні, сплави WC-TaC-TiC-Со із 1932 до 1950 застосовувалися тільки в США. У післявоєнні роки ці матеріали здобули панівне становище в обробці сталі. Сплави системи WC-TiC-Со здебільшого застосовуються для обробки сталей на високих швидкостях різання. Сплави з невеликими домішками карбіду титану можна застосовувати й для обробки матеріалів, що дають стружку надлому.
Дефіцитність і висока вартість вольфраму зумовили необхідність створення та впровадження у виробництво нових, безвольфрамових сплавів, які не поступались би за властивостями промисловим металам марок ВК, ТК і ТТК. Використання безвольфрамових сплавів дозволить більшою мірою задовольнити зростаючі потреби різних галузей в якісних інструментальних матеріалах.
Карбід титану, що має високу твердість і низьку густину, становить особливий інтерес як замінник карбіду вольфраму. Перші промислові тверді сплави на основі карбіду титану являли собою твердий розчин TiC-Мо2С зі зв'язуючими металами, що містять 10-15% Ni, Ni-Cr, Ni-Мо або Ni-Мо2С[30]. Ці тверді сплави не здобули промислового застосування насамперед через високу крихкість і низьку міцність. Однак після досліджень, що виявили значний вплив на властивості безвольфрамових твердих сплавів змочуваності карбіду титану рідкою фазою, ці сплави знову привернули увагу дослідників. Вміст молібдену в сплавах значно зменшили й частково або повністю вводили його в металеву зв'язку у вигляді NiMo, а як тверду складову використовували TiC[30].
Загалом розроблені зараз безвольфрамні тверді сплави за твердістю і зносостійкістю дещо перевершують тверді сплави на основі WC, а за міцністю наближаються — до них, мають високу жароміцність і корозійну стійкість.
Велику групу матеріалів на основі карбіду титану являють карбідосталі, які за властивостями й призначенням посідають проміжне положення між швидкорізальними сталями й твердими сплавами. Карбідосталі в деяких випадках навіть перевершують тверді сплави за зносо- і термостійкістю, пластичністю. Цей клас матеріалів має найнижчий коефіцієнт тертя в порівнянні з будь-якими зносостійкими матеріалами, що застосовуються в промисловості зараз.
Карбідосталі поєднують твердість і зносостійкість карбіду титану з добрими механічними властивостями сталі, наявність якої дає можливість виконувати термічну обробку. Склад сталей обирається з таким розрахунком, щоб отримати потрібні фізичні та технологічні характеристики. Залежно від необхідних властивостей змінюється не тільки склад карбідосталі, а й технологія виготовлення виробів, особливо важливими в цьому аспекті є стадії спікання й термічної обробки.
Карбідосталі добре проявили себе в різних галузях промисловості, зоврема в автомобільній та авіаційній промисловості. Висока зносостійкість цього матеріалу дозволяє успішно використовувати його для виготовлення деталей машин: кулачків, сідел клапанів, деталей вальниць і т. д. З карбідосталей виготовляють елементи токарних верстатів, зносостійкість яких перевищує в 15-20 разів зносостійкість роликів зі швидкорізальної сталі[31].
Протягом багатьох років успішно експлуатуються інерціальні системи наведення ракет в літаках, забезпечені опорними валами, муфтами з карбідосталей[32].
Карбід титану є одним з найефективніших матеріалів, що використовується як зносостійке покриття. Це пов'язано насамперед з тим, що TiC найбільше задовольняє вимогам, які пред'являються до покриттів: високі зносостійкість і твердість при високих і низьких температурах; хороша хімічна стабільність; невеликий коефіцієнт тертя, хороше зчеплення з поверхнею матеріалу — основи; жаротривкість; мала схильність до холодного зварювання; здатність не руйнуватися під впливом механічних і теплових навантажень.
Крім того карбід титану застосовується і в більш складних багатокомпонентних комплексних покриттях. Зокрема встановлено, що при хромотитануванні сталі У8А безпосередньо до основи примикає шар карбіду хрому[ru] Cr7C3 товщиною 8,0 мкм, а шар TiC з товщиною 7,0 мкм розташований із зовні. Аналіз отриманого покриття показав, що зміна мікротвердості в двошарових покриттях TiC–Cr7C3 порівняно з одношаровими TiC та Cr23C6–Cr7C3 від поверхні до основи більш плавна. Саме ця перевага багатокомпонентних покриттів порівняно з однокомпонентними буде позитивно впливати на стійкість покриттів в умовах контактної взаємодії[33].
Розроблені багатошарові покриття за участю сполук ТіС, TiN та оксиду алюмінію Al2O3. Певна комбінація шарів різних сполук в покритті може визначати необхідні властивості виробу. Знання та багаторічний досвід у використанні багатошарових покриттів для різальних інструментів дозволяють вибирати саме необхідний порядок розташування шарів.Так, комбінація ТіС, TiN, Al2O3 надає поверхні інструменту при експлуатації високотемпературну стабільність, стійкість до лункоутворення. Зумовлено це тим, що оксид алюмінію має серед згаданих сполук найкращу термічну і хімічну стабільність, але у порівнянні із карбідом титану невисоку твердість[34].
Карбід титану характеризується хімічною інертністю до багатьох матеріалів, високою твердістю та теплопровідністю. Більша теплопровідність TiC у порівнянні з традиційними абразивними матеріалами (алундом і карборундом) дозволяє обробку на більшій швидкості й виключає появу тріщин, припікання та інших макродефектів.
Зазвичай під час виготовлення паст із карбіду титану як сполучні й Поверхнево-активні речовини використовуються модифіковані ліпіди, різні вуглеводні та їх похідні, співвідношення яких змінюється залежно від конкретних умов застосування.
Статична абразивна здатність карбіду титану, яка в основному визначається мікротвердістю й міцністю частинок, перевищує абразивну здатність поширеного алунду й лише трохи поступається статичній абразивній здатності карбіду кремнію й дибориду кальцію[35].
Для всіх абразивних матеріалів зменшення розміру часток абразивного порошку призводить до зменшення абразивної здатності матеріалу. Для карбіду титану між цими характеристиками спостерігається прямолінійна залежність[36].
Першими магнітно-абразивними матеріалами (МАМ) були порошки матеріалів із магнітними властивостями і досить високою твердістю для здійснення абразивного різання (ферити, альсифер і т. д.), а останнім часом розроблені композиційні МАМ, які значно переважають однорідні за абразивною здатністю. Композиційні МАМ складаються з феромагнітної та абразивної складових. Як перша найбільше застосування знайшло залізо. До абразивної складової висунуті такі вимоги: високі твердість і крихкість, слабка взаємодія з феромагнітною основою при температурах синтезу МАМ.
МАМ на основі системи Fe-TiC мають найкращі магнітні та абразивні властивості серед традиційних магнітно-абразивних матеріалів[37].
Карбід титану нестехіометричного складу використовується як каталітичний матеріал при синтезі аміаку, в реакціях гідрогенізації і дегідрування, при виробництві хлору і каустику[38][39][40].
Серед карбідів тугоплавких металів TiC за каталітичною активністю поступається тільки карбіду вольфраму при реакціях гідрогенізації і дегідрогенізації сполук різних класів, наприклад при розкладанні перекису водню і циклогексану, гідрогенізації етилену[40], реакціях 1,2-хлорбутану і 1,2-бутанолу[41].
Карбід титану знайшов широке застосування як замінник графіту в електродах або як добавка до графіту. Електроди на основі карбіду титану використовують при кисневому різанні сталей під водою, електролізі водних розчинів, вакуумному випаровуванні алюмінію, електроконтактній обробці матеріалів, як термоелектроди термопар. Високі службові властивості електродів забезпечує хороша електропровідність карбіду титану в поєднанні з хімічною інертністю і непоганими характеристиками міцності.
Карбід титану є основним компонентом наконечників (захисних чохлів), що використовуються для ізоляції термоелектродів металевих термопар від хімічного, ерозійного і механічного впливу навколишнього середовища.
В умовах плавки кольорових металів та їх сплавів (міді, бронзи, латуні) в індукційних печах наконечник зі сплаву TiC — 20% Со, що використовується спільно з платинородій-платиновою термопарою, має вищу стійкість у розплаві, термостійкість і жаротривкість при температурах 1100 °C порівняно з наконечниками з молібдену та кераміки[10].
Висока стійкість карбіду титану в розплавах металів і їх сплавах привернула пильну увагу матеріалознавців. Тиглі на основі системи TiC-TiB2 отримали широке поширення для плавлення металів.
Висока структурна стабільність плівок системи TiC-Al2O3 забезпечує хорошу стабільність електроопору при високих температурах[42].
Останнім часом набуло поширення зміцнення карбідом титану сплавів алюмінію, нікелю, титану, сталі та міді[43].
Карбід титану вводиться в матрицю механічним легуванням або додаванням твердих частинок TiC в розплавлений метал. Однак не завжди цими методами вдається домогтися рівномірного розподілу зміцнювальної фази в матриці. Проте розроблений метод, який дозволяє усунути цей недолік[44]. Карбід титану вводиться в розплав за допомогою пневматичної гармати, і залежно від тиску газів в струмінь можна вводити в матрицю до 7% (об'ємних) TiC.
Введення в литий алюміній частинок карбіду титану є перспективним для збільшення міцності і пластичних властивостей алюмінієвих сплавів. Оптимальна кількість добавки карбіду титану становить 5%, так як подальше збільшення його вмісту приводить до незначного підвищення його властивостей[45].
Серед інших тугоплавких сполук карбід титану здійснює найбільший вплив на властивості литого алюмінію, сприяючи підвищенню не тільки міцності, а й пластичності[45].
Одноразове введення білим щурам 50 мг пилу TiC приводило до помірного потовщення міжальвеолярних перегородок, розростання сполучної тканини легень, посилення легеневого малюнку, гіперплазії лімфатичних фолікулів навколо бронхів і їх склерозу[46][47]. Вдихання пилу TiC протягом 5 місяців по 1 г на день у концентрації 400–800 мг/м3 викликало у щурів аналогічну реакцію в легенях.
Рекомендована гранично допустима концентрація карбіду титану становить 10 мг/м3[48].
- 7 // Вісник Академії наук Української РСР. — Київ : видавництво Академії, 1975.
- Хижняк В.Г., Дегула А.І., Лесечко Д.В. 4 // Металознавство та обробка металів. — Київ, 2009. — С. 20-24.
- Хижняк В.Г., Дегула А.І., Лоскутова Т.В., Курило Н.А. 49 // Проблеми тертя та зношування. — Київ, 2008. — Т. 2. — С. 66-70.
- 3 // Фізика і хімія твердого тіла. — Івано-Франківськ, 2004. — Т. 5. — С. 557—563.
- Кипарисов С.С., Левинский Ю.В., Петров А.П. Карбид титана: получение, свойства, применение. — Москва : Металлургия, 1987. — 216 с. (рос.)
- Вредные вещества в промышленности. Справочник для химиков, инженеров и врачей / Под. ред. Коц В. А., Либерман Н. Р., Томарченко С. Л. — 7. — Ленинград : Химия, 1977. — Т. 3. — С. 468-469. — 52000 прим. (рос.)
- Туманов В. И. Свойства сплавов системы карбид вольфрама-карбид титана-карбид тантала-карбид ниобия-кобальт. — Москва : Металлургия, 1973. — 184 с. (рос.)
- Свистун Л. И. Износостойкие спеченные композиционные материалы "металл-карбид титана". — Краснодар : КубГТУ, 2007. — 88 с. — ISBN 9785833302705. (рос.)
- LaSalvia J. C. Production of dense titanium carbide by combining reaction synthesis with dynamic compaction. — San Diego : University of California, 1990. — 292 с. (англ.)
- Krainer H. Physical Studies of Titanium Carbide and of Cemented Carbide Compositions Containing Titanium Carbide. — H. Brutcher, 1951. — 30 с. (англ.)
- ↑ Titanium, methyl-
- ↑ Дзодзиев Г. Т., Граков В. Е., Калъков А. А. и др. — Порошковая металлургия, 1975, № 9, с. 86-90. (рос.)
- ↑ Моисеев Г. К., Попов С. К., Овчинникова Л.A., Ватолин Н. А. — Известия АН СССР, Неорганические материалы, 1982, т. 18, № 9, с. 1521–1524. (рос.)
- ↑ Стасюк Л. Ф., Кислый П. С., Кузенкова М. А. и др. — Физика и техника высоких давлений, 1983, № 11, с. 13-15 (рос.)
- ↑ Стасюк Л. Ф., Кайдаш О. Н., Ткач В. П. — В кн.: Исследование и применение сверхтвердых и тугоплавких материалов. Киев: ОНТИ ИСМ АН УССР, 1981, с. 3-7 (рос.)
- ↑ Полищук B.C. — В кн.: Тугоплавкие соединения. Киев: ОНТИ ИПМ АН СССР, 1981, с. 23-29. (рос.)
- ↑ Yada К. — J. Electr. Microscopy, 1982, v. 31, № 4, p. 349–359. (англ.)
- ↑ Okaba J. — J. Ceram. Assoc. Jap., 1978, v. 86, № 11, p. 518–525. (англ.)
- ↑ Макаренко Г. Н., Миллер Т. Н. — В кн.: Карбиды и сплавы на их основе. Киев: Наукова думка, 1976, с. 5-9. (рос.)
- ↑ а б Косолапова Т. Я., Макаренко Г. Н., Зяткевич Д.Н — ЖФХО им. Д. И. Менделеева, 1979, т. 24, № 3, с. 328–333. (рос.)
- ↑ Богомолов А. М., Резвых В. Ф., Шуваев А.И и др. — В кн.: Дисперсные порошки и материалы на их основе. Киев: Наукова думка, 1982, с. 127–130. (рос.)
- ↑ Кипарисов С. С., Бескин А. Л., Петров А.И Переработка титанового скрапу. М., ЦНИИТЭИЦМ, 1984, 56 с. (рос.)
- ↑ Кипарисов С. С., Левинский Ю. В., Падалко О. В. и др. — Порошковая металлургия, 1985, № 8, с. 12-16. (рос.)
- ↑ Eiger G.W., Hunter W.L., Mauser J.E. — Bureau of mines of USA department of the interior. Report of investigations 8497, p. 1-20. (англ.)
- ↑ Асанов У. А., Джиенбекова A.A., Касымалиев A.K, Петренко Ю. Я. — Изв. АН Киргизской ССР, 1981, № 5, с. 46-47. (рос.)
- ↑ Chermant J. — L.-Rev. Int. Hautes Temper, et Refract., 1969, t. 6, p. 299–312. (англ.)
- ↑ Попов В. Е., Гурин В. Н. — В кн.: Карбиды и сплавы на их основе. Киев: Наукова думка, 1976, с. 21-26. (англ.)
- ↑ Wokulski Z., Wokulski K. — J. Cryst. Growth, 1983, v. 62, № 2, p. 439–446. (англ.)
- ↑ Sugiyama K., Mizuno H., Motojima S., Takahashi Y. — J. Cryst. Grouth, 1979, v. 46, p. 788–793. (англ.)
- ↑ Kato A., Tamari N. — J. Cryst. Browth, 1980, v. 49, p. 199–204. (англ.)
- ↑ Андриевский Р. А., Уманский Я. С. Фазы внедрения. М.: Наука, 1977, 240 с. (рос.)
- ↑ а б в Самсонов Г. В., Упадхая Г. Ш., Нешпор B.C. Физическое металловедение карбидов. Киев: Наукова думка, 1974. 455 с. (рос.)
- ↑ Подчерняева И. А., Симан Н. И., Фоменко B.C. — В кн.: Низкотемпературная плазма в технологии неорганических веществ. Новосибирск; Наука, 1971, с. 54-57. (рос.)
- ↑ Ковальченко М. С., Роговой Ю. И., Келим В. Д. — Атомная энергия, 1972, т. 32, № 4, с. 321–323. (рос.)
- ↑ Евтушенко O.B., Бурыкина A.A., Арчакова Г. Г. — Автоматическая сварка, 1970, № 2, с. 50-51. (рос.)
- ↑ Панчешная В. П., Княжева В. М., Клименко Ж. В., Антонова М. М. — Защита металлов, 1980, т. 16, № 6, с. 684–691. (рос.)
- ↑ Самсонов Г. В., Эпик А. П. Тугоплавкие покрытия. М.: Металлургия, 1973, 399 с. (рос.)
- ↑ а б Войтович Р. Ф. Окисление карбидов и нитридов. Киев: Наукова думка, 1981. 192 с. (рос.)
- ↑ Storf R. Industrie — Anzeiger, 1980, Bd. 102, № 46, S. 21-24. (нім.)
- ↑ а б Egan E.J. Jr. — Iron Age, 1959, v. 183, № 12, p. 101–105. (англ.)
- ↑ Гуревич Ю. Г., Фраге Н. Р., Савиных Л. М. — В кн.: Применение композиционных материалов на полимерных и металлической матрицах в машиностроении. Уфа, 1982, с. 27-29. (рос.)
- ↑ Ellis J.L. — Powder Metallurgy International, 1984, v. 16, № 2, p. 53-55.с (англ.)
- ↑ Хижняк В.Г. Комплексні зносостійкі покриття на основі тугоплавких сполук титану та хрому / В.Г. Хижняк, А.І. Дегула, Т.В. Лоскутова, Н.А. Курило // Проблеми тертя та зношування. – Київ. - 2008.- №49, Том 2. С. 66-70.
- ↑ Хижняк В.Г. Титаноалітування твердого сплаву ВК8 в закритому реакційному просторі // В.Г. Хижняк, А.І. Дегула, Д.В.Лесечко // Металознавство та обробка металів. –Київ.-2009.- №4. С. 20-24.
- ↑ Безыкорнов А. И., Богомолов Н. И., Гуринчик И. И. и др. — Порошковая металлургия, 1971, № 5, с. 65-69. (рос.)
- ↑ Попов В. Е., Вильк Ю. Н., Гурин В. Н., Чекрыгина ТМ. — Порошковая металлургия, 1981, № 8, с. 76-80. (рос.)
- ↑ Оликер В. Е., Жорняк А. Ф., Гридасова Т. Я. — Порошковая металлургия, 1983, № 10, с. 81-86. (рос.)
- ↑ Козлова Т. П., Митега А. П., Коваленко В. Н. и др. — Украинский химический журнал, 1976, № 5, с. 536–538. (рос.)
- ↑ Kharlamov А.I, Krivitskii V.P., Lemeshko N.D. — Reaction Kinetics and Catalysis Letters, 1981, v. 17, № 1-2, p. 63-67. (англ.)
- ↑ а б Kajima J., Miyazaki E., Inone Y. e.a. — Journal of Catalysis, 1979, v. 59, № 3, p. 472–474. (англ.)
- ↑ Шевченко C.A., Левлюк Л. П., Павлов C.M. — Порошковая металлургия, 1984, № 6, с. 1-7. (рос.)
- ↑ Осипов К. А., Борович Т. Л., Мирошкина ЕМ. и др. — В кн.: Исследование и применение сплавов тугоплавких металлов. М.: Наука, 1983, с. 185–188. (рос.)
- ↑ Батуринская Н. Л., Кальчук H.A., Сервецкая М. Г., Черный В. Г. — Изв. АН СССР. Металлы, 1983, № 3, с. 166–170. (рос.)
- ↑ Fleming R.P.M. — High Temperatures-High Pressures, 1982, v. 14,№ 2, p. 165–170. (англ.)
- ↑ а б Zielinski P.G., Ast D.G. — Journal of Materials Science Letters, 1983, № 2, p. 495–498. (англ.)
- ↑ Мигай К. Б. Научные труда институтов охраны труда ВЦСПС, 1969, вып. 61, с. 80—86. (рос.)
- ↑ Брахнова И. Т., Самсонов Г. В. Гигиена и санитария, 1970, № I, с. 42—45. (рос.)
- ↑ Брахиова И. Т. Токсичность порошков металлов и их соединений. Киев, «Наукова думка», 1971, с. 223. (рос.)
![]() | Ця стаття належить до добрих статей української Вікіпедії. |